濟南注塑加工中的收縮是注塑加工中很常見的一個問題,尤其是對表面質(zhì)量要求高的塑料制品。因此,隨著注塑加工技術(shù)的不斷提高,大限度地減少注塑加工的收縮,提高產(chǎn)品質(zhì)量勢在必行。
Shrinkage in injection molding is a common problem in injection molding, especially for plastic products with high surface quality requirements. Therefore, with the continuous improvement of injection molding technology, it is imperative to reduce the shrinkage of injection molding and improve the product quality.
在塑料零件較厚部分(如筋或突起)形成的收縮比相鄰部分更嚴重。這是因為較厚部分的冷卻速度比周圍區(qū)域慢得多。不同的冷卻速度會導(dǎo)致結(jié)合面形成凹陷,稱為縮痕。
Shrinkage formed in thicker parts of plastic parts (such as ribs or protrusions) is more severe than that in adjacent parts. This is because the cooling speed of the thicker part is much slower than that of the surrounding area. Different cooling speeds will lead to the formation of depressions on the joint surface, which is called shrinkage marks.
這種缺陷嚴重限制了塑料制品的設(shè)計和成型,尤其是大型厚壁制品如電視斜盒、展示盒等。實際上,家電等要求嚴格的產(chǎn)品是需要去除縮孔的,而玩具等一些表面質(zhì)量要求不高的產(chǎn)品,在注塑加工時是允許有縮痕的。
This defect seriously limits the design and molding of plastic products, especially large thick wall products such as TV slant boxes and display boxes. In fact, household appliances and other products with strict requirements need to remove shrinkage holes, while toys and other products with low surface quality requirements are allowed to have shrinkage marks during injection molding.
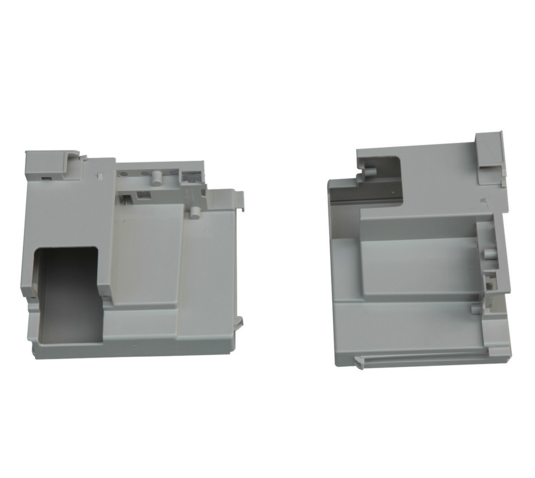
形成注塑加工縮痕的原因可能有一個或多個,包括加工方法、零件幾何形狀、材料選擇和模具設(shè)計等。幾何形狀和材料選擇通常由原材料供應(yīng)商決定,不能輕易改變。然而,在模具制造商中,有許多與模具設(shè)計相關(guān)的因素可能會影響注塑加工的收縮率。
There may be one or more reasons for forming shrinkage marks in injection molding, including processing method, part geometry, material selection and mold design. Geometry and material selection are usually determined by the raw material supplier and cannot be easily changed. However, in mold manufacturers, there are many factors related to mold design that may affect the shrinkage of injection molding.
冷卻流道、澆口類型和澆口尺寸的設(shè)計可能會產(chǎn)生不同的效果。例如,小型澆口,如管狀澆口,冷卻速度比錐形澆口快得多。澆口過早冷卻會減少型腔的填充時間,從而增加縮痕的可能性。
The design of cooling runner, gate type and gate size may have different effects. For example, a small gate, such as a tubular gate, cools much faster than a conical gate. Premature cooling of the gate will reduce the filling time of the cavity, thus increasing the possibility of shrinkage marks.
對于成型工人來說,調(diào)整加工條件是注塑加工中收縮問題的一種方法。填充壓力和時間顯著影響收縮率。
For molding workers, adjusting the processing conditions is a way to solve the shrinkage problem in injection molding. Filling pressure and time significantly affected the shrinkage.
零件填充后,多余的材料繼續(xù)填充到型腔中,以補償材料的收縮。如果填充階段過短,收縮會加劇,終會產(chǎn)生更多或更大的縮痕。這種注塑加工本身收縮的方法可能無法將縮痕減少到令人滿意的程度,但成型工人可以調(diào)整填充條件來改善縮痕。
After the part is filled, the excess material continues to fill into the cavity to compensate for the shrinkage of the material. If the filling stage is too short, the shrinkage will be intensified and more or larger shrinkage marks will be produced. This method of solving the shrinkage of the injection molding process itself may not reduce the shrinkage mark to a satisfactory degree, but the molding workers can adjust the filling conditions to improve the shrinkage mark.
This is the end of the notes on shrinkage during injection molding. You can visit our website http://m.wtkbt.com Consult more about the operation, attention and problems during injection molding.